The Ultimate Guide To Alcast Company
The Ultimate Guide To Alcast Company
Blog Article
Facts About Alcast Company Revealed
Table of ContentsAlcast Company Fundamentals ExplainedOur Alcast Company DiariesThe Ultimate Guide To Alcast CompanyOur Alcast Company StatementsExcitement About Alcast CompanyFascination About Alcast Company
The refined difference lies in the chemical content. Chemical Comparison of Cast Light weight aluminum Alloys Silicon advertises castability by lowering the alloy's melting temperature and enhancing fluidity throughout spreading. It plays a critical role in permitting intricate mold and mildews to be loaded precisely. Furthermore, silicon adds to the alloy's strength and wear resistance, making it important in applications where toughness is crucial, such as vehicle parts and engine components.It additionally enhances the machinability of the alloy, making it easier to refine right into ended up items. In this means, iron adds to the general workability of light weight aluminum alloys.
Manganese adds to the stamina of light weight aluminum alloys and boosts workability (Aluminum Castings). It is generally used in wrought aluminum items like sheets, extrusions, and profiles. The visibility of manganese aids in the alloy's formability and resistance to splitting during fabrication processes. Magnesium is a lightweight component that offers toughness and impact resistance to aluminum alloys.
Excitement About Alcast Company
It allows the manufacturing of light-weight elements with excellent mechanical buildings. Zinc boosts the castability of light weight aluminum alloys and assists manage the solidification process throughout casting. It boosts the alloy's strength and solidity. It is commonly located in applications where intricate forms and great details are needed, such as decorative castings and specific automotive components.
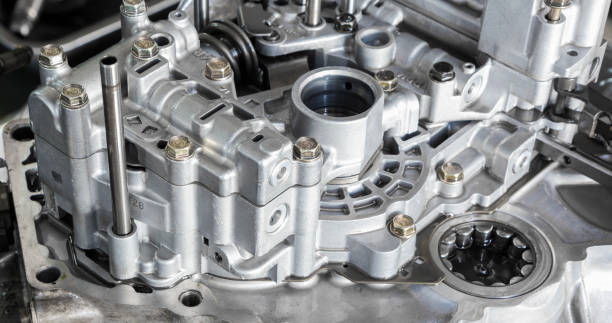
The key thermal conductivity, tensile stamina, return stamina, and elongation differ. Amongst the above alloys, A356 has the highest possible thermal conductivity, and A380 and ADC12 have the least expensive.
Our Alcast Company Ideas

In accuracy spreading, 6063 is appropriate for applications where complex geometries and premium surface area coatings are extremely important. Examples consist of telecommunication rooms, where the alloy's exceptional formability enables sleek and cosmetically pleasing styles while keeping structural integrity. In the Lights Solutions industry, precision-cast 6063 components create sophisticated and reliable lights components that need elaborate shapes and great thermal performance.
It causes a better surface finish and far better rust resistance in A360. The A360 exhibits premium prolongation, making it optimal for complicated and thin-walled parts. In precision casting applications, A360 is well-suited for sectors such as Consumer Electronic Devices, Telecommunication, and Power Devices. Its improved fluidness permits detailed, high-precision components like smartphone casings and communication tool real estates.
The Of Alcast Company
Its special properties make A360 a valuable option for precision casting in these industries, improving item toughness and high quality. Light weight aluminum alloy 380, or A380, is a widely utilized spreading alloy with numerous unique characteristics. It offers exceptional castability, making it a suitable selection for precision casting. A380 displays great fluidness when molten, making sure elaborate and detailed mold and mildews are precisely replicated.
In precision spreading, light weight aluminum 413 radiates in the Customer Electronic Devices and Power Tools sectors. It's typically made use of to craft complex elements like smart device housings, camera bodies, and power tool coverings. Its accuracy is remarkable, with tight resistances up to 0.01 mm, ensuring remarkable product setting up. This alloy's premium corrosion resistance makes it an exceptional choice for outside applications, guaranteeing resilient, durable items in the discussed industries.
Getting The Alcast Company To Work
The light weight aluminum alloy you select will significantly impact both the casting procedure and the homes of the last item. Due to the fact that of this, you must make your decision very carefully and take an educated approach.
Figuring out the most appropriate aluminum alloy for your application will certainly imply considering a broad variety of attributes. The first category addresses alloy features that influence the manufacturing process.
Not known Incorrect Statements About Alcast Company
The alloy you select for die spreading straight influences several elements of the casting process, like just how easy the alloy is to collaborate with and if it is prone to casting problems. Warm fracturing, likewise referred to as solidification breaking, is a normal die spreading issue for aluminum alloys that can lead to internal or surface-level tears or fractures.
Particular aluminum alloys are much more at risk to warm breaking than others, and your option ought to consider this. Another typical flaw found in the die casting of light weight aluminum is die soldering, which is when the click here for more info cast stays with the die walls and makes ejection challenging. It can harm both the actors and the die, so you need to look for alloys with high anti-soldering residential properties.
Corrosion resistance, which is currently a significant quality of light weight aluminum, can differ significantly from alloy to alloy and is a crucial characteristic to think about relying on the ecological problems your product will be exposed to (Aluminum Casting). Wear resistance is one more property commonly sought in light weight aluminum products and can differentiate some alloys
Report this page